In the fast-paced world of manufacturing, efficiency and precision are key. Pneumatic cylinders play a crucial role in automating various processes, but not all cylinders are created equal. Understanding the different types of pneumatic cylinders can significantly impact the performance of your machinery and systems. This article delves into the specifics of single-acting pneumatic cylinders, offering a comprehensive overview tailored for professionals in the manufacturing industry.
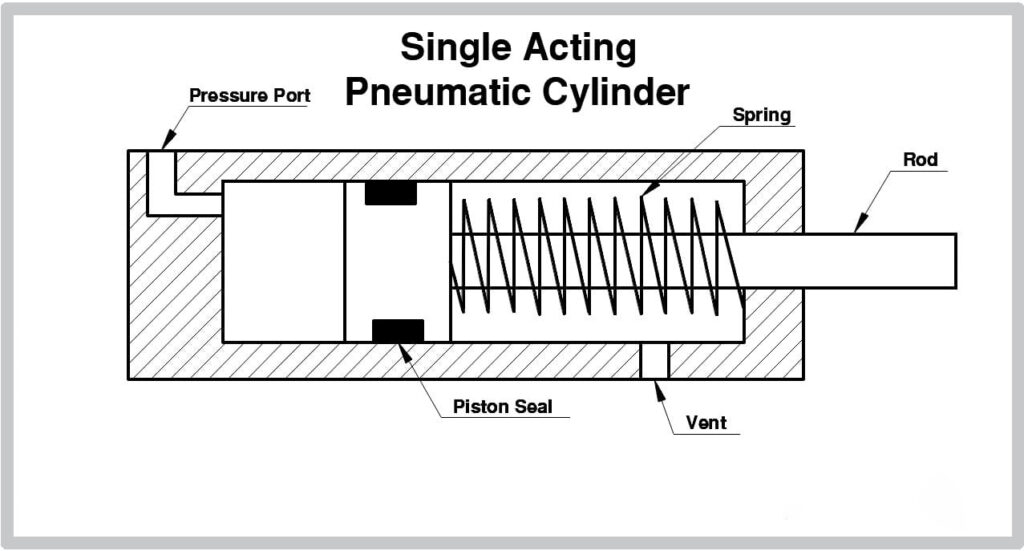
A single-acting pneumatic cylinder is an actuator that uses compressed air to move a piston in one direction. It has one port that allows compressed air to enter, causing the rod to extend. The return movement is typically powered by a spring or external force, rather than air pressure.
Let’s delve deeper into the specifics of single-acting pneumatic cylinders and understand their distinct features, advantages, and applications.
What is a Single Acting Pneumatic Cylinder?
A single-acting pneumatic cylinder operates by using compressed air to move a piston in one direction only. This type of cylinder has a single port for the air to enter. When air pressure is applied, the piston extends, performing the desired work. The retraction of the piston is usually achieved by a built-in spring or an external force such as gravity.
The design of a single-acting pneumatic cylinder is relatively simple, consisting of a cylinder barrel, a piston, a piston rod, end caps, and a return mechanism, which is often a spring. When compressed air enters the cylinder through the port, it pushes against the piston, causing the piston rod to extend. Once the air pressure is released or redirected, the return mechanism pulls the piston rod back to its original position.
Single-acting pneumatic cylinders are commonly used in applications where the work needs to be performed in one direction only, such as in clamping, lifting, or ejecting operations. Their simplicity and cost-effectiveness make them a popular choice in various industrial settings.
What is the Difference Between Single and Double-Acting Pneumatic Cylinders?
The primary difference between single-acting and double-acting pneumatic cylinders lies in their operational mechanics and capabilities.
- Single-Acting Pneumatic Cylinders: These cylinders use air pressure to extend the piston and rely on a spring or external force for retraction. They have a single port for air intake. Because air pressure is only used for one direction of movement, single-acting cylinders are simpler and more cost-effective. However, they are generally slower and less powerful compared to double-acting cylinders. Single-acting cylinders are ideal for applications where force is needed in one direction, such as clamping, lifting, or ejecting.
- Double-Acting Pneumatic Cylinders: These cylinders use air pressure for both extension and retraction of the piston. They have two ports, one for air intake to extend the piston and another for air intake to retract the piston. This dual operation makes double-acting cylinders faster, more powerful, and suitable for applications requiring precise control in both directions. Double-acting cylinders are commonly used in applications that demand high force and rapid movement, such as in robotics, automation systems, and material handling.
While double-acting cylinders offer greater control and efficiency, they are more complex and expensive than single-acting cylinders. The choice between single and double-acting cylinders depends on the specific requirements of the application, including the need for speed, force, and control.
What are the Advantages of a Single-Acting Cylinder?
Single-acting cylinders offer several advantages that make them suitable for various industrial applications:
- Simplicity: The design of single-acting cylinders is straightforward, with fewer components compared to double-acting cylinders. This simplicity translates to easier installation, maintenance, and troubleshooting.
- Cost-Effectiveness: Due to their simpler design and fewer components, single-acting cylinders are generally less expensive than double-acting cylinders. This cost advantage makes them an attractive option for applications where budget constraints are a consideration.
- Energy Efficiency: Single-acting cylinders use compressed air only for extending the piston. The return movement is powered by a spring or external force, which means less compressed air is required overall. This can lead to energy savings, particularly in applications where the cylinders are used frequently.
- Ideal for Specific Applications: Single-acting cylinders are perfect for tasks where force is only needed in one direction. For example, they are commonly used in clamping operations to hold objects in place, in lifting operations to elevate loads, and in ejecting operations to push parts off conveyor belts.
- Reliability: With fewer moving parts and a simpler design, single-acting cylinders tend to be more reliable and have a longer service life. They are less prone to mechanical failures and can withstand harsh industrial environments.
Despite these advantages, single-acting cylinders have some limitations, such as slower speed and lower force compared to double-acting cylinders. However, their benefits often outweigh these limitations in many industrial applications.
What is a Single Acting Pneumatic Cylinder Powered By?
Single-acting pneumatic cylinders are powered by compressed air. The operation of these cylinders involves the following steps:
- Air Intake: Compressed air is introduced into the cylinder through a single port. The air pressure builds up behind the piston, causing it to move.
- Piston Extension: As the air pressure increases, it pushes against the piston, forcing the piston rod to extend. This extension performs the desired work, such as lifting, clamping, or ejecting.
- Return Mechanism: Once the work is completed, the air pressure is released or redirected. The return movement of the piston rod is achieved through a built-in spring, gravity, or an external force. The spring or external force pulls the piston rod back to its original position, ready for the next cycle.
The efficiency and performance of single-acting pneumatic cylinders depend on the quality and consistency of the compressed air supply. Proper maintenance of the air supply system, including regular checks for leaks and ensuring clean and dry air, is essential for optimal cylinder operation.
Single Acting Pneumatic Cylinder Diagram
A typical diagram of a single-acting pneumatic cylinder includes the following parts:
- Cylinder Barrel: The main body of the cylinder, which houses the piston and other internal components. It is typically made of aluminum, stainless steel, or composite materials to withstand high pressures and provide durability.
- Piston: A movable component inside the cylinder barrel that separates the air chamber into two parts. The piston is connected to the piston rod and moves when compressed air is introduced.
- Piston Rod: A rod attached to the piston that extends and retracts as the piston moves. The piston rod transfers the linear motion of the piston to perform the desired work.
- End Caps: The end caps seal the cylinder barrel and provide mounting points for the cylinder. They also house the port for air intake and the return mechanism.
- Port for Air Intake: The port through which compressed air is introduced into the cylinder. It is typically located on one end cap.
- Return Spring: A spring mechanism that pulls the piston rod back to its original position once the air pressure is released. The spring is housed inside the cylinder barrel or attached externally.
Understanding the components and their functions is crucial for the proper installation, maintenance, and troubleshooting of single-acting pneumatic cylinders.
Single Acting Pneumatic Cylinder Symbol
In pneumatic schematics, the single-acting cylinder is represented by a rectangle with one arrow indicating the direction of air flow and a spring symbol denoting the return mechanism. The symbol typically includes the following elements:
- Rectangle: Represents the cylinder barrel.
- Arrow: Indicates the direction of air flow into the cylinder.
- Spring Symbol: Denotes the presence of a return spring that pulls the piston rod back to its original position.
Understanding the schematic symbols is essential for interpreting pneumatic diagrams and ensuring the correct installation and operation of pneumatic systems.
Single Acting Pneumatic Cylinder Specifications
When selecting a single-acting pneumatic cylinder for a specific application, several key specifications should be considered:
- Bore Size: The diameter of the cylinder barrel. The bore size determines the force output of the cylinder. A larger bore size provides greater force but requires more air pressure.
- Stroke Length: The distance the piston travels from its fully retracted to fully extended position. The stroke length should be chosen based on the required movement for the application.
- Operating Pressure: The maximum and minimum air pressure required for the cylinder to operate effectively. The cylinder should be compatible with the pressure range of the compressed air supply system.
- Material: The material of the cylinder components, such as the barrel, piston, and piston rod. Common materials include aluminum, stainless steel, and composite materials. The material should be chosen based on the operating environment and required durability.
- Mounting Options: Various mounting configurations are available, such as flange mounts, foot mounts, and pivot mounts. The mounting option should be selected based on the installation requirements and available space.
Selecting the appropriate specifications ensures that the cylinder performs efficiently and reliably in the intended application.
Single Acting Pneumatic Cylinder vs Double
Comparing single-acting and double-acting pneumatic cylinders highlights their respective strengths and weaknesses:
- Single-Acting Pneumatic Cylinders: These cylinders use air for extension and a spring or external force for retraction. They are simpler, cheaper, and more energy-efficient but offer slower speeds and lower force compared to double-acting cylinders. Single-acting cylinders are suitable for applications where force is needed in one direction only.
- Double-Acting Pneumatic Cylinders: These cylinders use air for both extension and retraction, providing greater control, speed, and force. They are more complex and expensive but are ideal for applications requiring precise and rapid movement in both directions. Double-acting cylinders are commonly used in automation systems, robotics, and material handling.
The choice between single-acting and double-acting cylinders depends on the specific requirements of the application, including the need for speed, force, control, and cost considerations.
Applications of Single Acting Pneumatic Cylinders
Single-acting pneumatic cylinders are used in various industrial applications where force is needed in one direction only. Some common applications include:
- Clamping: Single-acting cylinders are used to hold objects in place during machining or assembly operations. The cylinder extends to apply clamping force and retracts once the operation is complete.
- Lifting: Single-acting cylinders are used to elevate loads in assembly lines or material handling systems. The cylinder extends to lift the load and retracts once the load is moved to the desired location.
- Ejection: Single-acting cylinders are used to push parts off conveyor belts or out of molds. The cylinder extends to eject the part and retracts once the part is removed.
- Positioning: Single-acting cylinders are used to move objects to a specific position in automated systems. The cylinder extends to move the object and retracts once the object is in place.
The simplicity, cost-effectiveness, and reliability of single-acting cylinders make them a popular choice for these and other applications.
Maintenance and Troubleshooting
Regular maintenance and timely troubleshooting are essential for the optimal performance and longevity of single-acting pneumatic cylinders. Key maintenance tasks include:
- Inspection: Regularly inspect the cylinder and its components for signs of wear and tear, such as scratches on the piston rod or leaks around the seals.
- 潤滑: Ensure that the moving parts of the cylinder, such as the piston and piston rod, are well-lubricated to reduce friction and prevent wear.
- Seal Replacement: Replace worn or damaged seals to prevent air leaks and ensure efficient operation. Common seals that may need replacement include piston seals, rod seals, and end cap seals.
- Cleanliness: Keep the cylinder and the surrounding area clean to prevent contamination. Dirt and debris can cause wear and damage to the cylinder components.
Common troubleshooting tips for single-acting pneumatic cylinders include:
- Air Leaks: Check for air leaks around the seals and connections. Leaks can reduce the efficiency of the cylinder and cause erratic movement.
- Slow Movement: Inspect the air supply system for issues such as low pressure or obstructions in the air lines. Ensure that the cylinder is properly lubricated and that the piston and rod are moving freely.
- Incomplete Stroke: Ensure that the air pressure is within the specified range and that there are no mechanical obstructions preventing the piston from fully extending or retracting. Check the return spring for proper function and replace if necessary.
Regular maintenance and prompt troubleshooting can prevent costly downtime and extend the service life of single-acting pneumatic cylinders.
Cost and Availability
Single-acting pneumatic cylinders are widely available from various manufacturers and suppliers. The cost of these cylinders depends on several factors, including the bore size, stroke length, material, and brand. Generally, single-acting cylinders are more affordable than double-acting cylinders due to their simpler design and fewer components.
When purchasing single-acting pneumatic cylinders, it is important to consider the following:
- Specifications: Ensure that the cylinder meets the required specifications for the intended application, including bore size, stroke length, operating pressure, and material.
- Quality: Choose cylinders from reputable manufacturers known for producing high-quality and reliable products. Look for certifications and industry standards that guarantee the performance and durability of the cylinders.
- Availability: Check the availability of the cylinders and any necessary accessories, such as mounting brackets or fittings. Some suppliers offer quick shipping options for in-stock items, which can be crucial for minimizing downtime in industrial settings.
- Support: Consider the level of technical support and customer service provided by the supplier. Reliable support can be invaluable for troubleshooting and ensuring the proper installation and operation of the cylinders.
By considering these factors, you can select the right single-acting pneumatic cylinders for your application and ensure they provide reliable and efficient performance.
Summary
In summary, single-acting pneumatic cylinders are essential components in many manufacturing processes. Their simplicity, cost-effectiveness, and efficiency make them suitable for various applications where force is needed in one direction. Understanding their operational mechanics, advantages, and maintenance requirements can significantly enhance their performance and lifespan. By selecting the right specifications and ensuring regular maintenance, you can maximize the benefits of single-acting pneumatic cylinders in your industrial operations.