Pneumatische cilinders, ook bekend als luchtcilinders, zijn cruciale onderdelen in automatiseringssystemen die perslucht omzetten in mechanische beweging. Inzicht in hun werking is essentieel voor het optimaliseren van prestaties in industriële toepassingen. Dit artikel gaat in op de mechanica, typen en toepassingen van pneumatische cilinders en biedt professionals een gedetailleerde gids.
A pneumatic cylinder operates by increasing internal pressure as compressed air enters one side of the cylinder. This pressure rise moves the piston in a specific direction, with the piston rod transmitting the developed force to move an object. The working fluid in pneumatic cylinders is compressed air.
To fully grasp the functionality of pneumatic cylinders, it’s important to explore their types, components, and working principles.
Pneumatic cylinders, often referred to as air cylinders, are widely used in automation systems to convert compressed air energy into mechanical motion. Their simple design, ease of maintenance, and cost-effectiveness make them a popular choice in various industries, including manufacturing, automotive, and robotics.
2. Basic Principles of Pneumatic Cylinders
The operation of pneumatic cylinders is based on the principles of fluid dynamics and pressure. Compressed air is used as the working fluid to exert force on a piston, causing it to move in a linear or rotary fashion. This movement is harnessed to perform a variety of tasks, such as lifting, pushing, pulling, and rotating objects.
Pressure and Force
The force exerted by a pneumatic cylinder is a result of the pressure applied to the piston area. The relationship between pressure (P), force (F), and area (A) is given by the equation: F=P×A Where:
- F is the force exerted by the cylinder,
- P is the pressure of the compressed air,
- A is the area of the piston.
3. Types of Pneumatic Cylinders
Pneumatic cylinders come in various types, each designed to meet specific application requirements.
Single-acting Cylinders
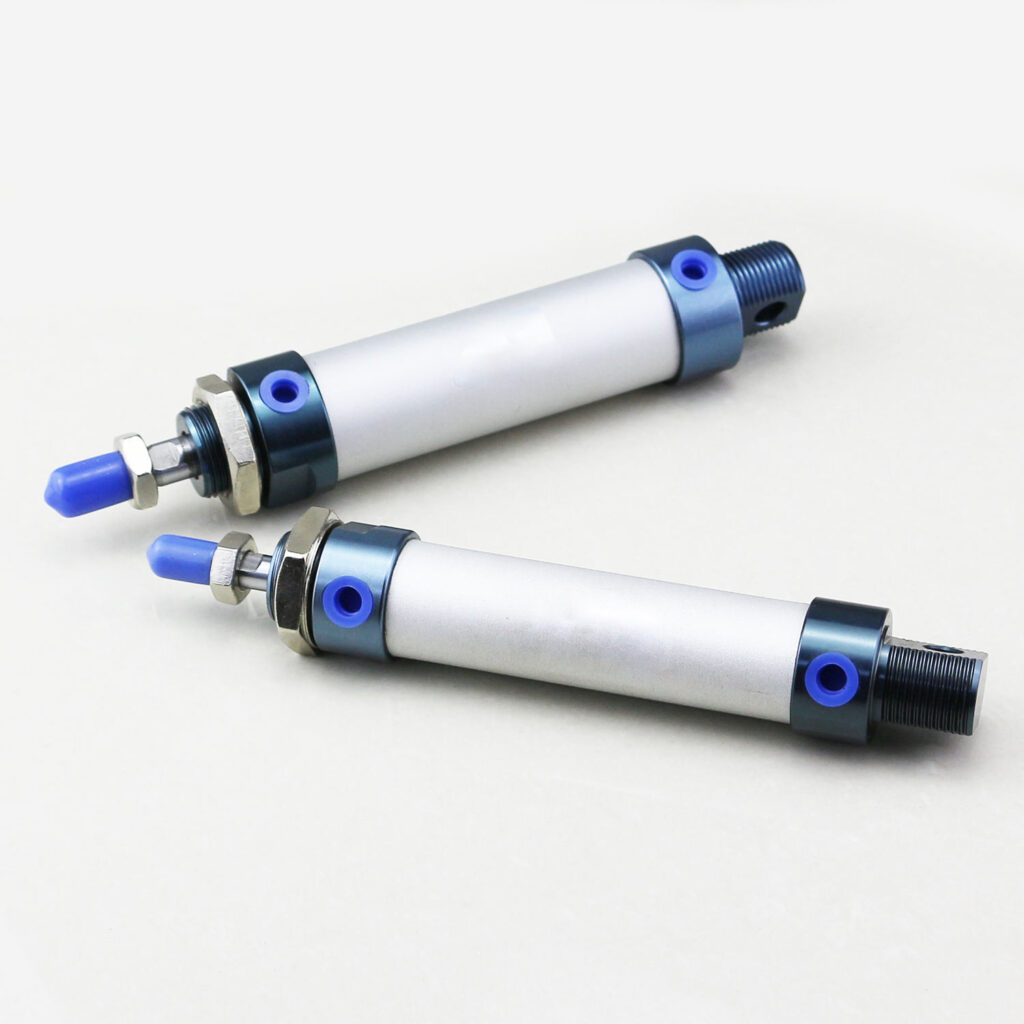
Single-acting cylinders use compressed air to move the piston in one direction only. A spring or external force returns the piston to its original position. They are suitable for applications where only one direction of movement is needed, such as in clamping or positioning.
Double-acting Cylinders

Double-acting cylinders use compressed air to move the piston in both directions. They have two ports: one for air to enter and extend the piston and another for air to retract it. These cylinders are ideal for applications requiring continuous movement in both directions, providing better control and efficiency.
Telescoping Cylinders
Telescoping cylinders feature multiple stages that extend in a telescoping manner, allowing for a longer stroke length compared to their retracted length. They are useful in applications where space is limited but a long stroke is needed, such as in lifting and material handling.
Rodless Cylinders
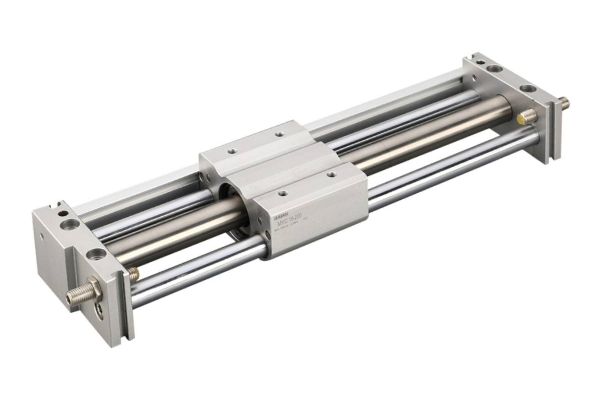
Rodless cylinders have the piston connected to a carriage that runs along the outside of the cylinder. This design allows for a more compact setup and eliminates the need for a piston rod, making them ideal for applications with space constraints.
Rotary Cylinders
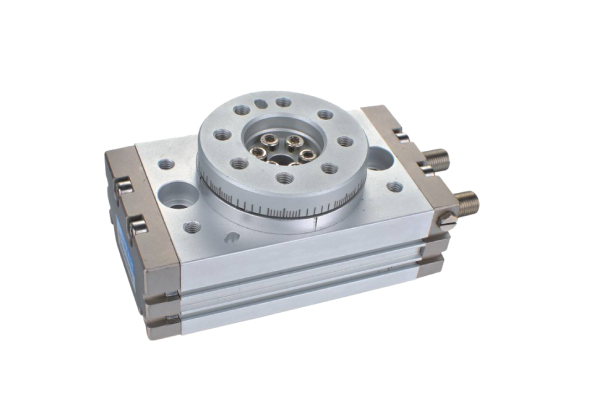
Rotary cylinders convert compressed air into rotary motion instead of linear motion. They are used in applications requiring rotational movement, such as turning, indexing, or positioning.
4. Components of Pneumatic Cylinders
Understanding the components of pneumatic cylinders is essential for proper maintenance and troubleshooting.
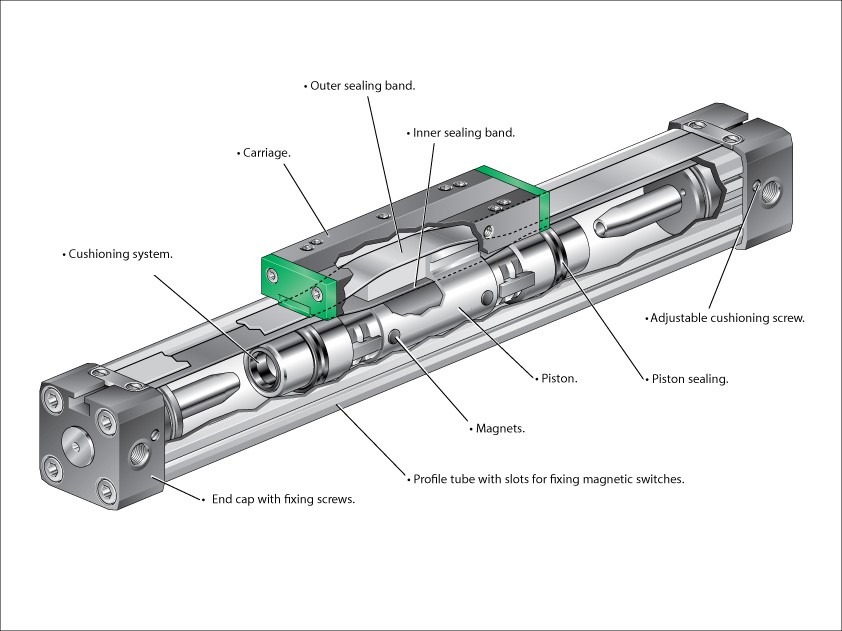
Cylinder Barrel
The cylinder barrel is the main body of the pneumatic cylinder, housing the piston and providing a sealed environment for the compressed air to act upon the piston. It is typically made of materials such as aluminum, steel, or stainless steel for durability and resistance to wear.
Piston
The piston is the moving part inside the cylinder that converts the air pressure into mechanical force. It is fitted with seals to prevent air leakage and ensure smooth movement within the barrel.
Piston Rod
The piston rod transmits the force generated by the piston to the external load. It is usually made of steel or stainless steel and is designed to withstand high levels of stress and wear.
End Caps
End caps seal the ends of the cylinder and contain ports for the compressed air to enter and exit. They also provide mounting points for the cylinder.
Seals
Seals prevent air leakage and ensure efficient operation of the cylinder. Different types of seals are used in various parts of the cylinder, including piston seals, rod seals, and end cap seals.
Cushions
Cushions are used to reduce the impact at the end of the piston stroke, protecting the cylinder and the load from damage. They are typically adjustable to control the cushioning effect.
5. Physics of Pneumatic Cylinders
The operation of pneumatic cylinders is governed by the principles of fluid dynamics and thermodynamics. When compressed air enters the cylinder, it increases the internal pressure, which exerts force on the piston. According to Pascal’s law, this pressure is exerted uniformly in all directions, causing the piston to move.
The force generated by the piston can be calculated using the formula: F=P×AF = P \times AF=P×A Where:
- FFF is the force,
- PPP is the pressure,
- AAA is the piston area.
This relationship highlights the importance of maintaining the correct pressure and ensuring the seals are in good condition to prevent air leakage and maintain efficiency.
6. How Pneumatic Cylinders Work: Step-by-Step
Understanding the working principles of pneumatic cylinders involves examining the operation of both single-acting and double-acting cylinders.
Single-acting Pneumatic Cylinder
A single-acting pneumatic cylinder has one port for compressed air to enter. The air pressure pushes the piston in one direction, extending the piston rod. When the air is released, a spring or external force returns the piston to its original position.
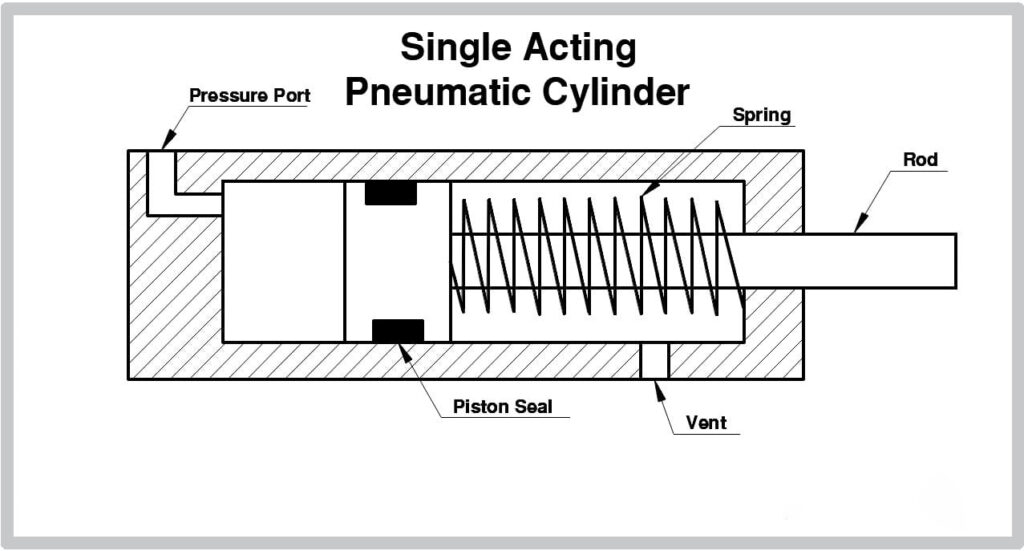
- Air Intake: Compressed air enters the cylinder through the port.
- Piston Movement: The air pressure pushes the piston, extending the piston rod.
- Air Release: The air is released, allowing the spring or external force to return the piston to its original position.
Double-acting Pneumatic Cylinder
A double-acting pneumatic cylinder has two ports: one for air to enter and extend the piston and another for air to retract it. This allows for continuous movement in both directions.

- Air Intake (Extension): Compressed air enters through the first port, pushing the piston and extending the piston rod.
- Air Release (Extension): The air is released through the second port.
- Air Intake (Retraction): Compressed air enters through the second port, pushing the piston in the opposite direction and retracting the piston rod.
- Air Release (Retraction): The air is released through the first port.
7. Applications of Pneumatic Cylinders in Automation
Pneumatic cylinders are used in a wide range of applications in automation, including:
- Material Handling: Moving and positioning materials on conveyor systems.
- Clamping and Holding: Securing workpieces in place during machining or assembly.
- Lifting and Lowering: Raising and lowering heavy objects in manufacturing processes.
- Pushing and Pulling: Applying force to move objects in a linear fashion.
- Rotating: Providing rotary motion for tasks such as indexing or positioning.
8. Advantages and Disadvantages
Pneumatic cylinders offer several advantages, including:
- Simplicity: Simple design and easy to maintain.
- Cost-Effectiveness: Generally cheaper than hydraulic or electric systems.
- Speed: Capable of rapid movement.
- Safety: Use of compressed air reduces the risk of fire or explosion.
However, they also have some disadvantages:
- Limited Force: Lower force output compared to hydraulic cylinders.
- Air Compressors: Require an air compressor, which can be noisy and require maintenance.
- Precision: Less precise control compared to electric actuators.
9. Maintenance and Troubleshooting
Proper maintenance and troubleshooting are essential for ensuring the longevity and efficiency of pneumatic cylinders.
Maintenance Tips
- Regular Inspection: Check for leaks, wear, and damage regularly.
- Lubrication: Ensure moving parts are adequately lubricated to reduce wear.
- Seal Replacement: Replace worn or damaged seals promptly.
- Air Quality: Use clean, dry air to prevent contamination and corrosion.
Troubleshooting Common Issues
- Air Leaks: Check and replace seals if necessary.
- Slow Movement: Check for obstructions, inadequate air supply, or worn components.
- Sticking Piston: Inspect and clean the cylinder, and check for bent rods or damaged seals.
- Inconsistent Operation: Ensure proper air pressure and check for leaks or blockages in the air supply.
10. Future Trends in Pneumatic Cylinder Technology
Advancements in materials, design, and control systems are driving the evolution of pneumatic cylinders. Some future trends include:
- Smart Cylinders: Integration of sensors and IoT technology for real-time monitoring and predictive maintenance.
- Energy Efficiency: Development of more energy-efficient designs to reduce air consumption and operating costs.
- Compact Designs: Miniaturization of components to allow for more compact and versatile applications.
- Advanced Materials: Use of advanced materials for improved durability and performance.
11. Conclusion
Understanding how pneumatic cylinders work is vital for optimizing their use in automation systems. By leveraging compressed air, these devices provide reliable and efficient motion control. For further insights and resources, stay tuned to our expert articles.